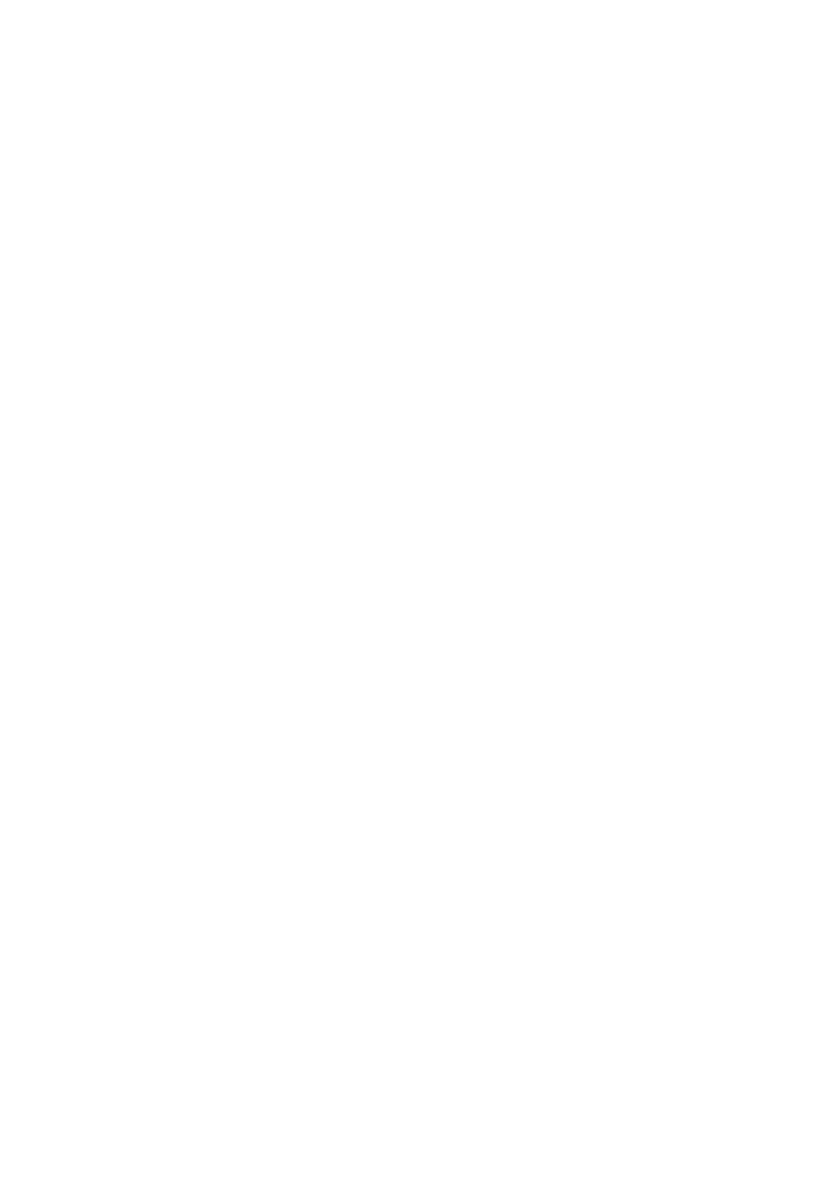
Original instructions IB-307
> English
Electric Installation
Nominal voltage 27,2V DC, measured at the
cable connections of the motor.
Voltage range: 16 – 32V DC
The motor can withstand excessive voltage
or excessive ambient temperature as long as
they are within the given ranges. However,
both excessive voltage and ambient
temperature will have a negative impact on
the service life of the pump.
In rush current
• When connecting the main power
supply, red lead to positive (+) terminal
and black lead to negative (-) terminal
the capacitors will become charged.
Approx. 300A during 1,3 ms.
• Current is limited electronically to 17,5A.
Fuse: Recommended fuse size 25 – 30A.
Cable connections
• Red to positive terminal (+),
wire size AWG 12.
• Black to negative terminal (-),
wire size AWG 12.
• White, control cable, Vin 0-10V or PWM
(see item Speed control below),
wire size AWG 16.
• Blue, speed signal, Tacho out,
12 ppr (pulses per revolution) 0 – 5V
used to register pump speed,
wire size AWG 16.
The motor has a built in polarity protection to
avoid damage if wrongly connected.
In order to start pump, supply nominal
voltage at main power supply, red cable +
and black cable - and >2V – 32V at white
control cable.
Voltage range for main power supply
(red + and black – cable) 16 – 32V DC.
Use of a relay for start/stop function is not
recommended.
Notes!
-Before installation with electrical control systems,
check that equipment to be used is of sufficiently rated
capacity to accept ampere draw of motor, 17,5 Amp.
- Voltage >35V may cause damage to the electronics.
-In order to avoid voltage transients, a battery should
be included in the power supply circuit.
-In order to obtain flammability according to UL94
Class V0, the separate wires must not be exposed.
Three Connection Alternatives
1. Three wire connection
• Connect red and white wire to plus
terminal (+).
• Connect black wire to negative
terminal (-).
• Tacho out signal is available at
blue wire, 12 ppr (pulses per revolution),
0 – 5V.
• The pump will operate at full speed.
• Speed control only available by variation
of supply voltage, 16- 32V.
2. Four wire connection/sleep mode/
speed control
• See image 3, page 13.
• Using this alternative, full voltage is
required at main power supply (red (+)
terminal and black (-) negative terminal).
• The pump starts up at voltage at white,
control wire, >2V. At voltage <2V pump
stops and goes into sleep mode. Power
consumption at sleep mode is 6,5 mA.
• Pump speed can be controlled by
Vin >2V and <10V at the white control
wire. At voltage >10V at the control wire
pump runs at full speed.
PWM signal into white cable is also
useful in order to control speed.
• Tacho out signal is available at
blue wire, 12 ppr (pulses per revolution),
0 – 5V.
• Max Voltage for Vin = 32V on white
control wire.
3. Connection/control via an external
Micro controller
• See Image 4, page 13.
Speed control
• In order to start up the pump, supply
nominal voltage at main power supply,
red (+) and black (-) and >2V – 32V at
white wire.
Analogue speed control
• White control wire.
• Vin 0 – 10V DC.
• 0 - <2V, no operation, sleep mode.
• >2V – 9,5V, pump operates with
constant speed, 2500 – 5750 rpm.
Example:
6 Vin; 400*4 (6-2) + 2500 =4100 rpm
(see Figure 8, Speed Map, Page 15)
• 10 to 32V, pump operates at full speed
• Speed control by Vin, approx. 400 rpm/V.
12