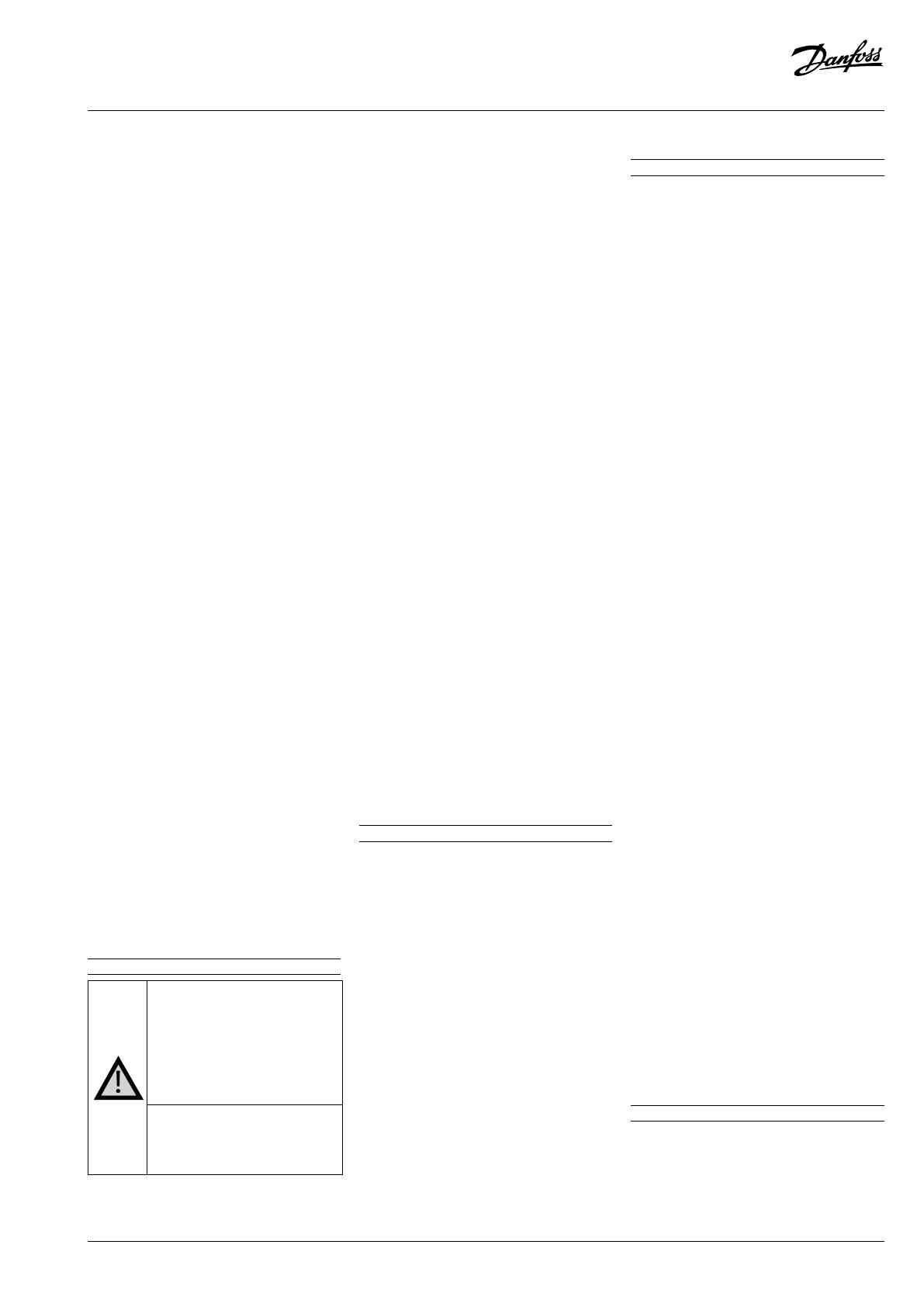
Anleitung
118A2177D - AN37261897352601-010401 | 11
© Danfoss | Climate Solutions | 2023.05
Start des Verdichters zu vermeiden. Nach Beendigung
der Einstellungen wieder anbringen.
Der elektronische Regler ist werksseitig auf R404A,
R449A, R452A oder R134a voreingestellt – je nach
eingebautem Verdichtertyp und Anwendung (siehe
Optyma™ Regler-Installationshandbuch 118U3808).
Bei Verwendung eines anderen Kältemittels muss die
Kältemitteleinstellung geändert werden.
• Halten Sie die obere Taste einige Sekunden lang
gedrückt. Daraufhin wird die Spalte mit den
Parametercodes eingeblendet.
• Der Parameter r12 muss vor der Änderung auf
0 gesetzt werden (der Software-Hauptschalter ist
ausgeschaltet (O)).
• Drücken Sie die obere oder untere Taste,
um zum Parametercode o30 zu navigieren.
• Halten Sie die mittlere Taste gedrückt, bis der Wert
für diesen Parameter angezeigt wird.
• Drücken Sie die obere oder untere Taste, um den
neuen Wert auszuwählen: 3 = R134a.17 = R507. 19
= R404A. 20 = R407C. 21 = R407A. 36 = R513A. 37
= R407F. 40 = R448A. 41 = R449A. 42 = R452A. 39 =
R1234yf. 51 = R454C. 52 = R455A
• Drücken Sie die mittlere Taste, um den ausgewählten
Wert zu bestätigen.
• Drücken Sie die obere oder untere Taste, um zum
Parametercode r84 zu navigieren. (r84 = maximal
zulässige Heißgastemperatur)
• Drücken Sie die mittlere Taste;
standardmäßig beträgt die maximal zulässige
Heißgastemperatureinstellung 125°C.
• Wenn der Kunde den Wert vergrößern möchte,
drücken Sie die obere Taste, um den neuen Wert
auszuwählen: 130°C. Drücken Sie die mittlere Taste,
um den ausgewählten Wert zu bestätigen.
• Die maximal zulässige Heißgastemperatur (r84) darf
130°C nicht überschreiten.
Die Optyma Plus 114X33YY und 114X43YY-Einheiten
sind mit einem EC-Lüftermotor ausgestattet. Der Optyma
Plus-ReglerparameterF17 wird hierfür auf 2 geändert,
um den 0-10-V-Ausgang der Lüfterdrehzahlregelung
zu aktivieren. Als Werkseinstellung ist der max.
LüfterdrehzahlparameterF19 auf 80% eingestellt, um
die Lüfterdrehzahl und die Geräuschemissionen in
Wohngebieten zu begrenzen. Anlagenbauer können
diese max. Drehzahl auf bis zu 100% erhöhen, wenn
die Geräuschemission keine Belästigung darstellt. Nur
bei Typen der Version P02 wird der Digitaleingang DI2
vom Regler an Modul B+ angeschlossen. Dies zeigt
den Alarm an, der bei einem Ausfall von ModulB+ den
Betrieb des Verdichters stoppt. Der Reglerparameter
o37 muss auf 1 eingestellt werden.
Die Drehzahländerung des EC-Lüftermotors wird
vom Optyma Plus Controller geregelt, indem die
Dierenz zwischen der Umgebungstemperatur
und der Tautemperatur gemessen wird. Je geringer
der Unterschied, desto höher ist die Drehzahl. Die
Werkseinstellung ist 8K. Der einstellbare Bereich beträgt
2–20K. Drücken Sie zum Einstellen auf dem Optyma-
Regler (der die gesättigte Verdampfungstemperatur
anzeigt) die mittlere Taste und ändern Sie den Wert mit
der oberen oder unteren Taste.
11. Abschließende Prüfung vor der Inbetriebnahme
Verwenden Sie gemäß den
allgemeinen und landesspezischen
Sicherheitsnormen und -vorschriften
Sicherheitsvorrichtungen, wie
Sicherheitsdruckschalter oder
mechanische Überdruckventile (nicht
mitgeliefert). Stellen Sie sicher, dass
sie funktionstüchtig und
ordnungsgemäß eingestellt sind.
Stellen Sie sicher, dass die Einstellungen
für die Hochdruckschalter und
Überdruckventile den maximalen
Betriebsdruck jeglicher Bauteile der
Anlage nicht überschreiten.
• Stellen Sie vor dem Starten des Verüssigungssatzes
sicher, dass die Sammlerventile und das
Kugelabsperrventil vollständig geönet sind.
• Vergewissern Sie sich, dass sämtliche elektrischen
Anschlüsse innen im Verüssigungssatz
ordnungsgemäß befestigt sind, da sie sich während
des Transports möglicherweise gelöst haben.
• Wenn eine Kurbelwannenheizung erforderlich ist,
muss diese mindestens 12 Stunden vor der ersten
Inbetriebnahme der Anlage eingeschaltet werden.
Dies gilt auch für Band-Kurbelwannenheizungen vor
einer erneuten Inbetriebnahme nach einer längeren
Stillstandszeit.
• Die Kurbelwannenheizung muss fest mit dem
Verdichtergehäuse verbunden sein. Stellen Sie
sicher, dass sie nicht herunterfällt und in der Luft
unter Spannung steht.
• Die Schaltschranktür muss mit dem Knauf
in der Türverkleidung fest verschlossen werden.
• Alle Verbindungsrohre mit dem Verüssigungssatz
Optyma™ Plus (Flüssigkeits- und Saugrohre) müssen
je nach Verdampferposition richtig dimensioniert
sein.
• Der Druckabfall in den Saug- und Flüssigkeitsleitungen
muss je nach Verdampferposition und -abstand
bewertet werden (siehe Coolselector2).
• Der Saug-/Heißgasdruck der Verüssigungs-
sätze Optyma™ Plus muss innerhalb des
Betriebsbereichs liegen. Der Verüssigungssatz
darf niemals betrieben werden, wenn der
Saugdruck unter dem absoluten Druck
(Vakuum) liegt.
• Die Einheit ist mit einem Hauptschalter mit Überlast-
und Kurzschlussschutz ausgestattet. Es wird jedoch
empfohlen, den Wert vor der Inbetriebnahme des
Verüssigungssatzes zu überprüfen. Den Wert für
den Überlastschutz nden Sie im Schaltplan auf der
Innenseite der Fronttür am Verüssigungssatz.
• Vergewissern Sie sich, dass der
Heißgastemperaturfühler fest sitzt und einen
ordnungsgemäßen Kontakt mit dem Heißgasrohr
hat.
• Stellen Sie sicher, dass Sie die Installations anleitung,
die mit dem Verüssigungssatz geliefert wird,
gelesen haben.
• Sie dürfen nur Kältemittel verwenden, die auf dem
Typenschild angegeben sind.
• Prüfen Sie den Ölstand des Verdichters.
• Prüfen Sie, ob alle Serviceventile geönet sind.
•
Stellen Sie sicher, dass der Hochdruckmessumformer
zur Anlage geönet ist.
• Prüfen Sie alle mechanischen Verbindungen auf
festen Sitz.
• Stellen Sie sicher, dass alle elektrischen
Überlasteinstellungen richtig eingestellt sind.
12. Inbetriebnahme
• Der Verüssigungssatz darf niemals ohne Kältemittel
betrieben werden.
• Alle Serviceventile müssen geönet sein.
• Das Rotalock-Ventil am Sammler sollte vollständig
geönet sein. Drehen Sie es gegen den
Uhrzeigersinn, um es vollständig zu önen.
• Prüfen Sie, ob der Verüssigungssatz für die
vorhandene Versorgungsspannung geeignet ist.
• Überprüfen Sie, ob die Kurbelwannenheizung
funktioniert.
• Überprüfen Sie, ob sich der Lüfter frei drehen kann.
• Überprüfen Sie, ob die Schutzfolie auf der Rückseite
des Verüssigers entfernt wurde.
• Gleichen Sie den Hoch-/Niederdruck aus.
• Schalten Sie den Verüssigungssatz ein.
Der Verüssigerlüfter muss sofort anlaufen
und nach 30 Sekunden Zeitverzögerung startet der
Verdichter (Vorbelüftung).
• Ob sich ein 3-Phasen-Verdichter in die falsche
Richtung dreht, lässt sich an folgenden Phänomenen
erkennen: Der Verdichter baut keinen Druck auf.
Der Verdichter arbeitet mit einem ungewöhnlichen
hohen Geräuschpegel. Die Leistungsaufnahme
des Verdichters ist ungewöhnlich gering. Bei
falscher Drehrichtung muss der Verdichter sofort
abgeschaltet werden um eine Korrektur zur richtigen
Phasenfolge herzustellen.
• Bei korrekter Drehrichtung ist an der Regleranzeige bzw. am
Niederdruckmanometer ein sinkender Druck abzulesen –
und an der Regleranzeige bzw. am Hochdruckmanometer
ein steigender Druck (nur beim Anlaufen).
13. Überprüfung bei laufendem Verflüssigungssatz
• Überprüfen Sie die Drehrichtung des Lüfters. Die Luft
muss vom Verüssiger zum Lüfter strömen.
• Überprüfen Sie Stromaufnahme und Spannung.
• Überprüfen Sie die Überhitzung der
Saugleitung, um das Risiko von Flüssigkeitsschlägen
zu vermindern.
• Sofern am Verdichter ein Schauglas vorhanden ist,
beobachten Sie den Ölstand beim Anlaufen und
während des Betriebs, um sicherzustellen, dass der
Ölstand sichtbar bleibt.
• Beachten Sie die Betriebsgrenzen.
• Die Verüssigungssätze Optyma™ Plus sind für den
Betrieb bis zu einer Umgebungstemperatur von
43 °C ausgelegt. Im Normal- oder Spitzenbetrieb darf
die Taupunktverüssigungstemperatur
für R404A/R507, R448A, R449A, R452A,
R454C, R455A 63°C nicht überschreiten. Die
Taupunktverüssigungstemperatur für R134a,
R513A und R1234yf darf 65 °C nicht überschreiten.
• Überprüfen Sie alle Leitungen auf ungewöhnliche
Vibrationen. Bewegungen von mehr als 0,15 mm
erfordern Korrekturmaßnahmen wie z. B. die
Verwendung von Rohrhalterungen.
• Bei Bedarf kann auf der Niederdruckseite in
größtmöglichem Abstand zum Verdichter üssiges
Kältemittel nachgefüllt werden. Während dieses
Nachfüllvorgangs muss der Verdichter in Betrieb
sein.
• Überfüllen Sie die Anlage nicht.
• Beachten Sie die in Ihrem Land geltenden
Vorschriften zum Recycling des Kältemittels aus dem
Verüssigungssatz.
• Lassen Sie niemals Kältemittel in die Atmosphäre
entweichen.
• Führen Sie eine allgemeine Inspektion der Installation
hinsichtlich Sauberkeit, Geräuschpegel und eine
Lecksuche durch, bevor Sie den Installationsort
verlassen.
• Dokumentieren Sie die Art und Menge des
Kältemittels sowie die Betriebsbedingungen als
Referenz für künftige Inspektionen.
• Prüfen Sie den Saug- und Heißgasdruck sowie die
Temperatur.
• Kältemittelfüllung und Laufströme von
Motoren zur Sicherstellung des ordnungsgemäßen
Betriebs.
• Überprüfen Sie die Überhitzung der
Saugleitung des Verdichters, um das Risiko
von Flüssigkeitsschlägen zu vermindern.
• Lassen Sie die Anlage 3-4 Stunden lang laufen.
Überprüfen Sie den Ölstand des Verdichters und
füllen Sie den richtigen Öltyp nach, wie auf dem
Typenschild von Verüssigungssatz und Verdichter
angegeben.
• Überprüfen Sie den Ölstand des Verdichters erneut
nach 24 Betriebsstunden.
• Führen Sie eine abschließende Leckageprüfung
durch, stellen Sie sicher, dass alle Abdeckungen
angebracht sind und alle Schrauben festgezogen
sind.
• Zur Einhaltung der vor Ort geltenden Normen
bringen Sie abschließend eine Kennzeichnung des
Kältemittels an.
• Scrollverdichter dürfen mit maximal 12 Start/
Stoppzyklen pro Stunde betrieben werden.
• Hubkolbenverdichter dürfen mit maximal 10 Start/
Stoppzyklen pro Stunde betrieben werden.
• Stellen Sie sicher, dass die Wartung entsprechend
den Installationsanweisungen durchgeführt wird.
14. Notbetrieb ohne Regler
Bei Ausfall des Reglers kann der Verüssigungssatz weiter
betrieben werden, sofern die Standardverdrahtung des
Reglers wie unten beschrieben modiziert und in eine
vorübergehende Verdrahtung geändert wird.