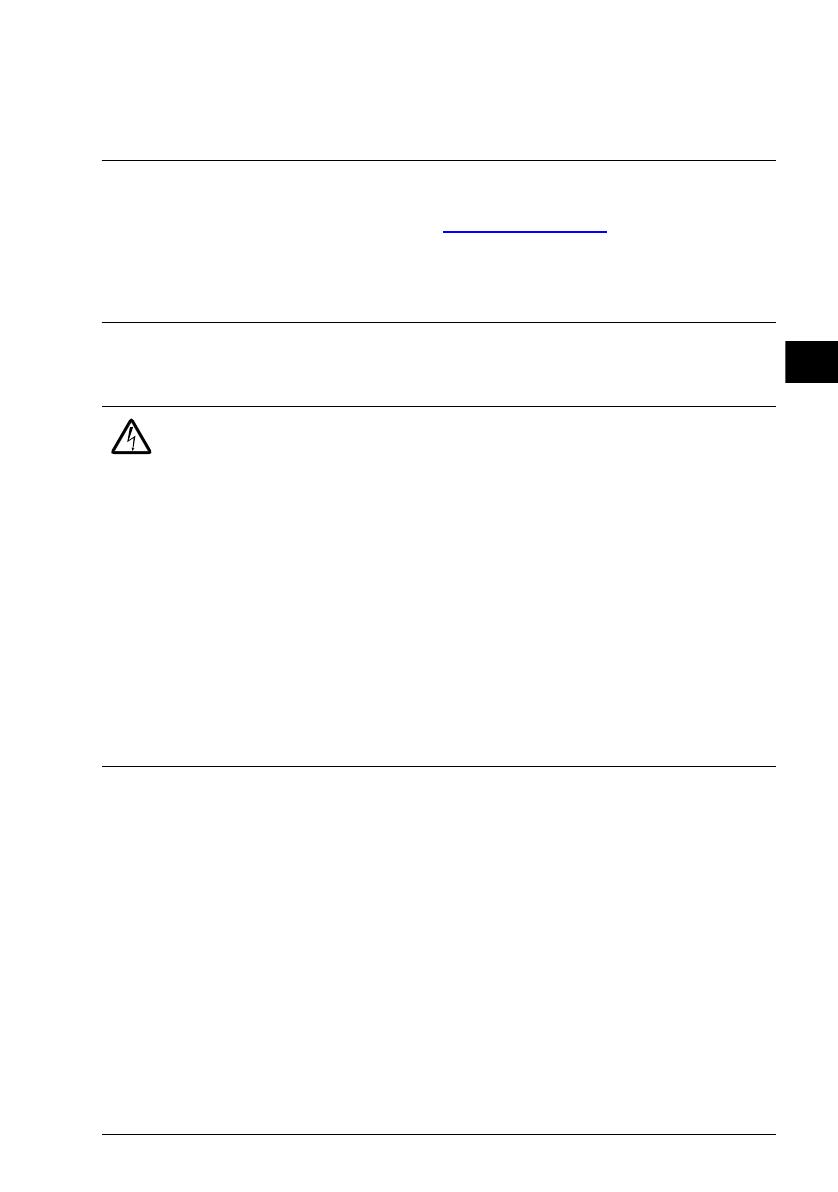
EN – Quick installation and start-up guide 7
EN – Quick installation and start-up
guide
This guide briefly instructs how to install and start-up the drive. For complete
information, see AS580-01 user’s manual (www.abb.com/drives
: Select Document
Library and search for document number 3AUA0000076333 [English]).
Installation
Obey the safety instructions
Check if capacitors need to be reformed
If the drive has been stored for a year or more, you must reform the capacitors.
You can determine the manufacturing time from the serial number, which you find on
the type designation label attached to the drive. The serial number is of format
MYYWWRXXXX. YY and WW tell the manufacturing year and week as follows:
YY: 13, 14, 15, … for 2013, 2014, 2015,
…
WW: 01, 02, 03, … for week 1, week 2, week 3, …
For information on reforming the capacitors, see Converter module capacitor
reforming instructions (3BFE64059629 [English]), available on the Internet.
WARNING! Obey these instructions. If you ignore them, injury or death, or
damage to the equipment can occur:
• If you are not a qualified electrician, do not do electrical installation work.
• Do not work on the drive, motor cable or motor when main power is applied. If
the drive is already connected to the input power, wait for 5 minutes after
disconnecting the input power.
• Do not work on the control cables when power is applied to the drive or to the
external control circuits.
• Make sure that debris from borings and grindings does not enter the drive when
installing.
• Make sure that the floor below the drive and the wall where the drive is installed
are non-flammable.